“We can no longer take things for granted.”
Interview with Kristina Edvinsson
The coronavirus has changed many things – including supply chains. What does this mean for Gelpell?
A lot of things that used to be taken for granted are now uncertain, requiring companies to be flexible and adopt a new approach. This not only affects supply chains, but also our own staff. Health has become a high risk factor and employee safety is our top priority. We had to deal with the question of how to guarantee an uninterrupted supply chain when large numbers of staff are off sick, for example.
Which delivery shortages affected Gelpell?
Since being established, Gelpell has maintained close partnerships with various European merchants and manufacturers. Be it raw materials, folding cartons or gelatin: we predominantly purchase our materials from manufacturers and merchants in Switzerland and Europe. This ensures professional handling, in particular, and – most importantly – reliable quality that meets high European standards. Thanks to this long-term strategy and loyalty, we can build on our close partnerships with our suppliers. This allowed us to deal with a lot of problems during the coronavirus crisis.
But of course we also had to contend with other, non-Covid-related delays in 2021. Some raw materials were held up in the Suez Canal, which was blocked by a grounded vessel for six days in March 2021. That impacted the entire supply chain for weeks. In addition, there were delivery shortages and price increases, for aluminium and paper, for example. Some raw materials were more difficult to obtain. And Brexit has also altered supply chains. The import and export of materials has become more complex and there are delivery problems in the UK in particular. There is a shortage of lorry drivers – a problem that has been exacerbated by Covid and differing entry requirements in different countries. Unfortunately, this lack of drivers cannot be resolved overnight.
How important is the supply chain for Gelpell?
Extremely important. For every customer order, we first of all check where the required raw materials of the appropriate quality and the right bulk density/particle size/concentration are coming from. We have always asked these questions, but now there is another important question: when will the raw materials be available? Prior to Covid, an uninterrupted supply chain was often taken for granted. Everything was always available, from anywhere, within a few days. That’s changed.
Consumers are also now increasingly quality-conscious. In the case of nutritional supplements, in particular, we are noticing that end customers are paying close attention to what they put into their bodies and where the products come from. Under pressure from consumers, the supply chain is also playing an increasingly important role here.
How are the current changes affecting demand?
These changes have created demand for flexible, intra-EU and local services. We are seeing a certain back-to-our-roots mentality and the desire for personal contact. Many companies no longer want to bear the risk of importing goods from afar. We are benefitting from that.
What advantages does Gelpell currently offer its customers?
We manufacture all our products at our own site in Gähwil – be it soft capsules, hard capsules, Gelpell beads, blister packs or jars. We benefit from our location in the middle of Europe and from short supply chains. As a Swiss producer, we are extremely committed to using high-quality raw materials. All our customers can visit our site and get an idea of our processes and quality. This was still possible during Covid, thanks to video audits and virtual production tours.
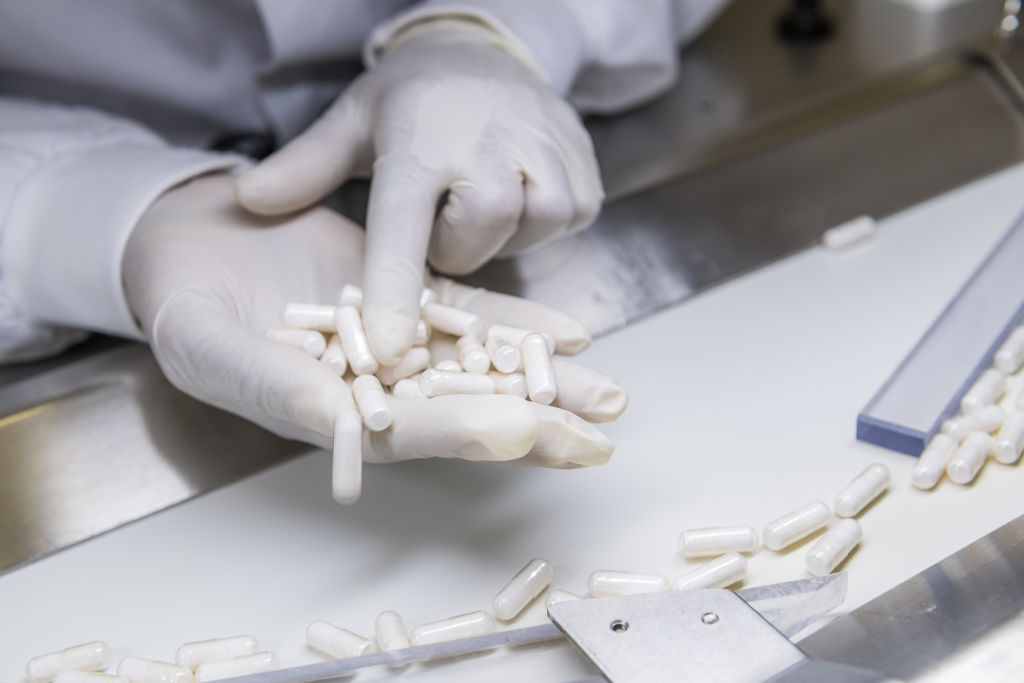

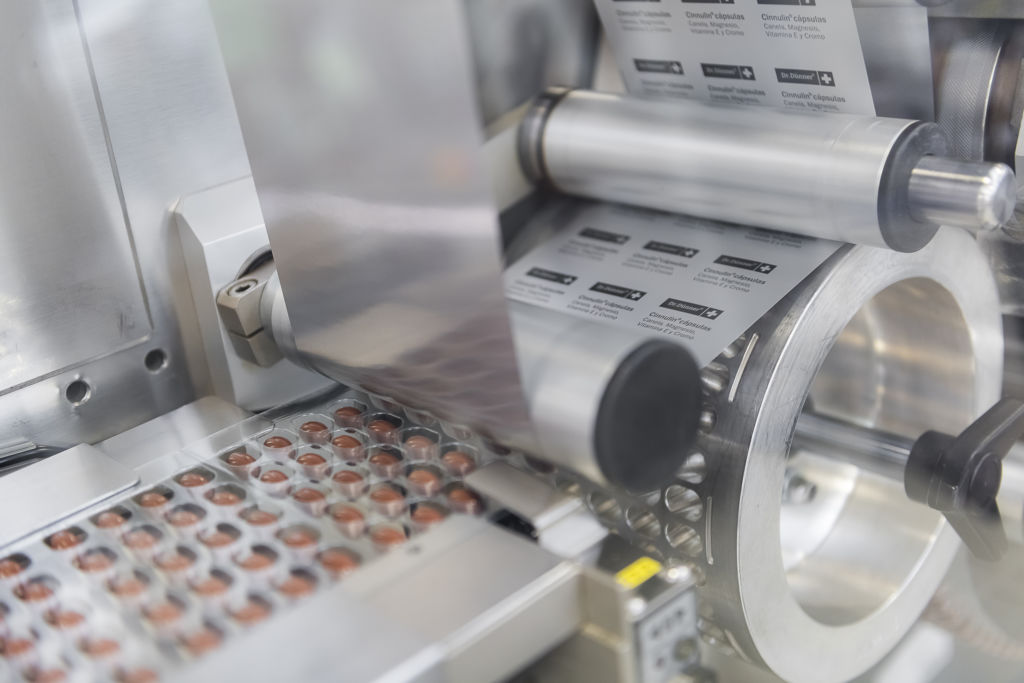